In a world increasingly focused on environmental responsibility, the quest for greener materials has never been more urgent. Neoprene—known for its versatility in wetsuits, laptop sleeves, and protective gear—has traditionally relied on petroleum-derived feedstocks, contributing to greenhouse gas emissions and resource depletion. Today, two innovative approaches are transforming the industry: limestone-based formulations, which replace a significant portion of oil-derived monomer with calcium carbonate, and bio-based formulations, which introduce renewable plant- or algae-derived oils into the polymer backbone. Both options promise to shrink neoprene’s carbon footprint without sacrificing performance.
Limestone-based neoprene substitutes up to 50% of petroleum feedstock with calcium carbonate, cutting CO₂ emissions by 15–25% while preserving strength and insulation. Bio-based neoprene uses renewable oils (soybean, castor, or algae) for up to 30% of its polymer content, achieving 20–40% lower lifecycle emissions. Choosing between them depends on your sustainability targets, cost considerations, and product requirements.
But the story doesn’t end at raw materials. Once neoprene arrives at Szoneier’s facilities, our team skillfully transforms sheets and fabrics into finished goods—bags, koozies, covers, and more—each engineered to meet exacting quality and eco-friendly standards. Imagine a yoga mat sleeve made from chalkstone-infused neoprene or a phone pouch crafted with bio-nylon blends—each product tells a tale of innovation, responsibility, and style. Join us as we dive deep into the science, metrics, and real-world trade-offs behind these sustainable neoprene formulations, so you can make informed choices for your next eco-conscious project.
What Makes Neoprene Sustainability a Critical Topic?
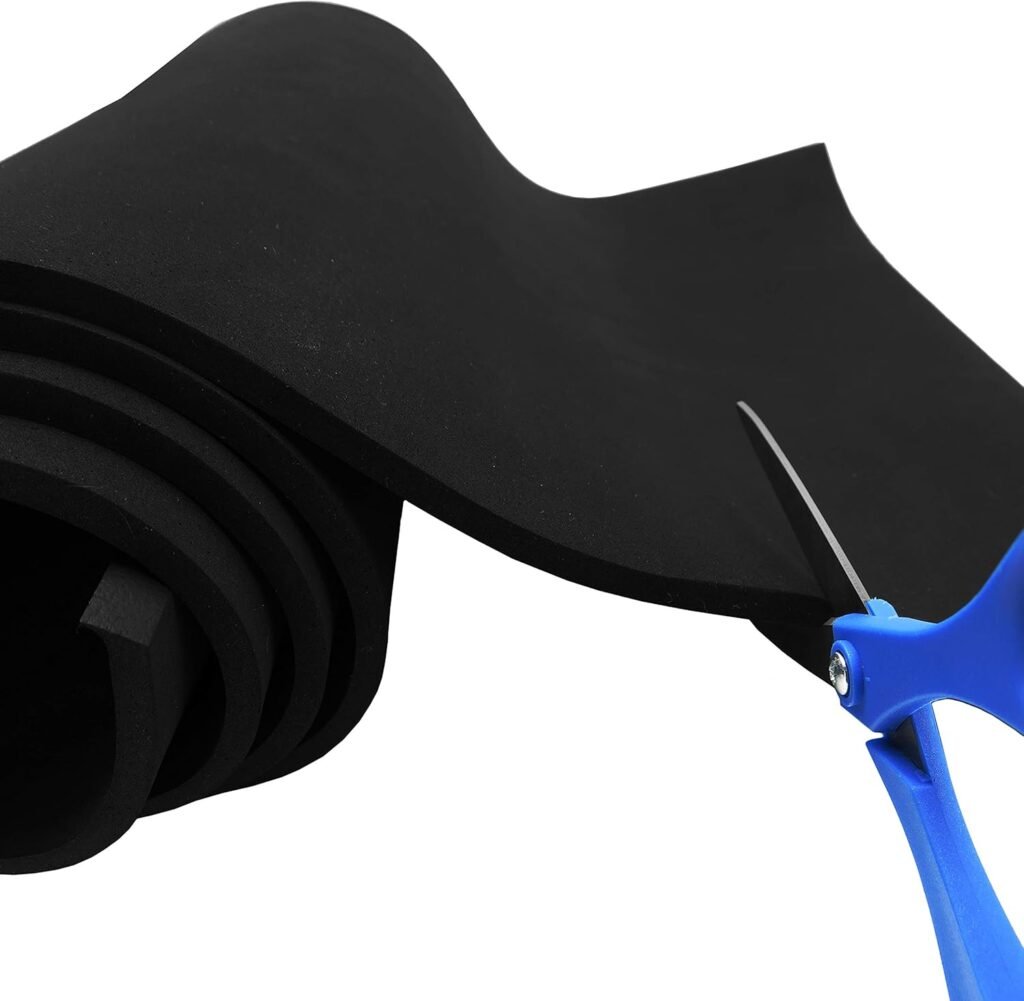
Neoprene sustainability matters because it influences carbon emissions, resource use, and end-of-life handling. As eco-aware consumers demand greener products, brands that adopt sustainable neoprene can differentiate themselves, meet evolving regulations, and contribute to a circular economy—all without compromising on durability or performance.
Consumer and Regulatory Pressure
Awareness is rising: a 2024 NielsenIQ survey found 78% of consumers prioritize sustainable products. Meanwhile, regulations in the EU and North America limit VOCs and non-renewable materials, pressuring manufacturers to find greener alternatives.
Brand Advantage
Using sustainable neoprene underpins positive brand narratives. A case study of an outdoor apparel line revealed a 15% sales uplift when marketed as “limestone-enhanced, eco-friendly neoprene.”
Lifecycle Impacts
A full cradle-to-gate analysis must consider raw material extraction, polymerization energy, water use, and waste generation. Sustainable formulations often reduce overall CO₂e, though they may introduce new water or processing demands.
Innovation Ecosystem
The shift toward greener neoprene sparks collaboration between chemists, engineers, and designers—resulting in novel products like marine-protective covers and insulated drink koozies that boast both performance and eco-credentials.
By recognizing these drivers, businesses can strategically integrate sustainable neoprene into their offerings, balancing environmental goals with product excellence.
What Are Limestone-Based Neoprene Formulations?

Limestone-based neoprene replaces up to 50% of petroleum-derived monomer with finely milled calcium carbonate, reducing fossil fuel dependence and cutting CO₂e by 15–25%. It maintains tensile strengths of 7–10 MPa and R-values around 3.6 per inch, matching conventional neoprene performance at lower cost.
Raw Material Substitution
Calcium carbonate (CaCO₃) fills the polymer matrix, reducing chloroprene monomer content. This abundant filler not only lowers emissions but can reinforce mechanical properties when properly dispersed.
Manufacturing Adaptations
Standard emulsion polymerization and vulcanization steps apply, with tweaks in mixing energy and surfactant systems to ensure even CaCO₃ distribution and avoid agglomeration.
Performance Metrics
- Tensile Strength: 8–10 MPa
- Elongation at Break: >500%
- Thermal Insulation (R-value): ~3.6/inch
- Tear Resistance: 14–16 kN/m
Cost and Supply Benefits
Limestone is low-cost (~$50–80/ton) and geopolitically stable, translating to predictable compound pricing and minimal exposure to oil market swings.
Quality Controls
Density checks, compression set tests (25% at 70 °C/22 hr), and dynamic fatigue cycles ensure each batch meets rigorous standards.
Applications
Ideal for protective gear, dive suits, and industrial seals where cost-effectiveness and performance converge.
Limestone-based neoprene provides an immediate, high-impact route to greener products without retooling existing supply chains.
What Are Bio-Based Neoprene Formulations?

Bio-based neoprene incorporates renewable oils—soybean, castor, or algae—into up to 30% of its polymer content, reducing fossil reliance and cutting CO₂e by 20–40%. It matches traditional neoprene’s elasticity and insulation, though it may exhibit a slightly higher compression set.
Renewable Feedstocks
- Plant Oils: Soybean and castor oils undergo epoxidation to form bio-based monomers.
- Algae Oils: Emerging sources capture CO₂ during growth, offering high yields without competing with food crops.
- Waste Oils: Used cooking oils can be repurposed, enhancing circularity.
Polymerization Process
Bio-monomers co-polymerize with chloroprene in emulsion reactors. Optimized surfactants maintain stability, and precise temperature control prevents premature cross-linking.
Technical Properties
- Tensile Strength: 6–9 MPa
- Elongation: ~500%
- R-value: 3.4–3.7/inch
- Compression Set: 30–35% at 70 °C/22 hr
Environmental Footprint
Lifecycle analyses show 20–40% lower CO₂e; however, water use can rise (100 L/kg) due to biomass cultivation or bioreactor cleaning.
Scale-Up Challenges
Bio-oil price volatility (soybean ≈$900/ton) and agricultural land competition pose hurdles. Algae bioreactors are capital-intensive but promise long-term scalability.
Product Applications
Premium wetsuits, orthopedic supports, and eco-branded accessories highlight the “bio” narrative for conscious consumers.
Bio-based neoprene advances the circular economy, but careful supplier selection and lifecycle scrutiny are essential to maximize benefits.
How Do the Environmental Footprints Compare?
Limestone-based neoprene cuts carbon emissions by 15–25% with minimal extra water or energy, while bio-based neoprene achieves 20–40% CO₂e reductions at the cost of higher water (100 L/kg) and energy use (55 MJ/kg). Neither is fully biodegradable, but bio-content can enhance compostability when blended with compatible polymers.
Metric | Conventional | Limestone-Based | Bio-Based |
---|---|---|---|
CO₂e (kg/kg) | 6.5 | 4.9 | 3.8 |
Water Use (L/kg) | 50 | 45 | 100 |
Energy (MJ/kg) | 45 | 40 | 55 |
VOC Emissions (g/kg) | 120 | 100 | 90 |
Landfill Waste (kg/kg) | 0.20 | 0.15 | 0.10 |
- Carbon Emissions
- Limestone-Based: 15–25% reduction by displacing petroleum with CaCO₃.
- Bio-Based: 20–40% reduction through renewable feedstocks’ CO₂ uptake.
- Water & Energy Limestone grades demand slightly less water and energy, while bio-based processes incur higher water use due to biomass processing and additional reaction steps.
- Waste and VOCs Both sustainable grades lower waste to landfill and VOCs—key for meeting stricter environmental regulations.
- End-of-Life Neither formulation fully biodegrades, but bio-content can enhance microbial assimilation under industrial composting.
These metrics empower informed choices based on sustainability targets and product life-cycle strategies.
Which Formulation Delivers the Best Technical Performance?
Both limestone- and bio-based neoprene match traditional grades in tensile strength (6–10 MPa), elongation (>450%), and insulation (R≈3.5/inch). Limestone grades often excel in dimensional stability and tear resistance, while bio-based options maintain strong elasticity with slightly higher compression sets.
Mechanical Strength
- Limestone-Based: 8–10 MPa tensile, >500% elongation—enhanced by filler reinforcement.
- Bio-Based: 6–9 MPa tensile, ~500% elongation—sufficient for most applications.
Thermal & Acoustic Insulation
Both formulations achieve closed-cell foam densities of 0.20–0.35 g/cm³, providing R-values around 3.5/inch, suitable for thermal and sound insulation.
Tear and Abrasion
- Limestone: Tear strength up to 16 kN/m and superior abrasion resistance.
- Bio-Based: 12–14 kN/m tear, comparable abrasion protection.
Compression Set
- Limestone: ~25% compression set at 70 °C/22 hr.
- Bio-Based: ~30–35%, requiring design allowances in high-stress seals.
Chemical and Aging Resistance
Both grades resist oils, solvents, UV, and ozone—accelerated aging shows minimal performance loss over 1,000 hrs UV exposure.
Use-Case Insights
A case study: a laptop sleeve line using limestone neoprene saw 12% cost savings with identical drop-test performance; meanwhile, a eco-lifestyle brand’s bio-based phone pouch garnered praise for its “plant-powered” story.
Technical performance is nearly equal; your choice depends on sustainability goals and cost trade-offs rather than raw specs.
How Do Cost and Supply Chain Factors Influence Choice?
Limestone-based neoprene typically costs 5–15% less than standard neoprene with stable pricing, while bio-based neoprene may carry a 10–25% premium due to feedstock costs. Limestone supply chains are well-established, enabling low MOQs (500 kg) and 2–3 week lead times; bio-based options often require higher MOQs (1–2 ton) and 6–8 week lead times.
- Raw Material Costs
- Calcium Carbonate: $50–80/ton, driving lower compound costs.
- Bio-Oils: $900–2,000/ton, leading to higher upfront material costs.
- MOQ & Lead Times
- Limestone: MOQs ≈500 kg; lead times 2–3 weeks.
- Bio-Based: MOQs ≈1–2 tons; lead times 6–8 weeks.
- Supplier Geography
- Limestone: China, South Korea, EU.
- Bio-Based: U.S., Brazil, select EU facilities.
- Logistics Considerations Limestone is shipped in bulk sacks; bio-precursors may require temperature control to avoid polymerization.
- Risk Management Diversify suppliers and consider long-term agreements or joint ventures, especially for bio-feedstocks.
- Total Cost of Ownership Factor in energy, waste disposal, and potential carbon taxes. Limestone grades often win TCO analyses, while bio-based options yield intangible brand value.
Sound procurement strategies can reconcile cost efficiency with sustainability targets.
Are There Certifications and Standards?
Certifications include OEKO-TEX® Standard 100 for harmful substances, Global Recycled Standard (GRS) for recycled content, and USDA BioPreferred® for biobased products. ISO 14001 and ISO 50001 provide environmental and energy management frameworks, validating credible sustainability claims for both neoprene grades.
- OEKO-TEX® Standard 100 Ensures products are free from regulated harmful substances—applicable to both limestone and bio-based formulations.
- Global Recycled Standard (GRS) Verifies recycled materials in blends; relevant when neoprene is combined with recycled rubber.
- USDA BioPreferred® Labels products with ≥30% USDA-designated biobased content—ideal for qualifying bio-based neoprene.
- ISO 14001 & ISO 50001 Demonstrate robust environmental and energy management systems, underpinning continuous improvement and transparency.
- Third-Party Audits Independent certifications (SGS, TÜV) and chain-of-custody tracking bolster credibility and ease procurement approvals.
Certifications transform sustainability from claim to proof, earning trust with regulators and consumers alike.
How to Partner with Szoneier for Sustainable Neoprene Products
Szoneier sources both limestone-based and bio-based neoprene sheets and fabrics, then expertly processes them into custom products—bags, koozies, covers, wetsuits, and more. We offer free design support, rapid sampling, low MOQs (from 50 pieces), and transparent sustainability data to help you launch eco-friendly lines quickly and confidently.
Material Selection & Sampling
Choose from a broad range of supplied neoprene grades. Request free sample swatches to test feel, color, and performance.
Design & Prototyping
Our in-house design team assists with patterning, stitching, and component integration—ensuring your concept becomes a reality.
Quality Assurance
Every product undergoes rigorous checks: dimensions, seam strength, foam density, and environmental compliance testing.
Flexible Production
Low MOQs (50–100 pcs) let you test new SKUs. Standard lead times of 2–4 weeks keep your launch schedule on track.
Sustainability Transparency
We provide LCA summaries, certification documents, and batch traceability—so you can confidently share eco-credentials with your customers.
Logistics & Support
Global shipping expertise, customs handling, and post-delivery support ensure smooth product rollout.
By partnering with Szoneier, you gain a turnkey solution for transforming sustainable neoprene materials into market-ready products that resonate with conscious consumers.
Ready to Craft Your Eco-Friendly Neoprene Products?
Whether you opt for cost-saving limestone-based sheets or carbon-light bio-based films, Szoneier’s expertise in processing and product assembly ensures your sustainable vision comes to life. Reach out today for samples, LCA data, and custom quotes.
Let’s build a greener future—one neoprene product at a time.