Rubber materials power countless industrial, marine, automotive, and consumer products—yet few debates are as heated among engineers and purchasing managers as Neoprene vs NBR (nitrile butadiene rubber). With over 18 years of neoprene R&D and manufacturing expertise, Szoneier understands that selecting the right elastomer can make or break product performance, longevity, and cost efficiency.
Imagine you’re designing a custom waterproof pouch for harsh marine environments. You need reliability, UV stability, and oil resistance—but you’re also under budget pressure and facing a tight lead time. Do you pick Neoprene for its balanced performance? Or NBR for its superior chemical resistance?
Neoprene offers broader temperature and weather resistance, while NBR excels in oil and fuel resistance—choose based on your environment and cost targets.
The right choice requires balancing mechanical properties, chemical stability, aging resistance, and total cost of ownership. In a moment, we’ll explore an engaging case study where a leading marine electronics brand saved 25% on warranty claims by switching from NBR seals to Neoprene in their waterproof housings. But first, let’s dive into what makes each rubber unique—and why the “Neoprene vs NBR” question remains a cornerstone for OEM, private label, and OEM/ODM purchasers worldwide.
What Are Neoprene and NBR (Nitrile Butadiene Rubber)?
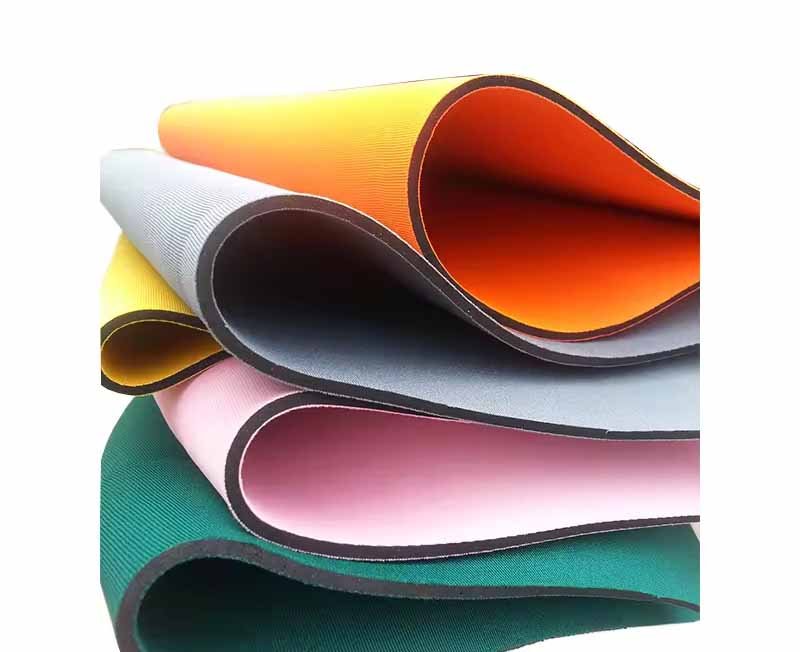
Neoprene is a chlorine-based synthetic rubber known for its balanced resistance to weather, ozone, and heat. NBR (nitrile butadiene rubber) is a copolymer prized for its superior resistance to oils, fuels, and solvents. While both share elastic properties, they differ fundamentally in chemical structure—Neoprene contains chlorine for weather resistance, whereas NBR’s acrylonitrile content boosts hydrocarbon resistance.
Neoprene (polychloroprene) was first commercialized in the 1930s to replace natural rubber and has since become ubiquitous in wetsuits, industrial seals, and protective gear. Its backbone of chloroprene monomers gives it inherent resistance to ozone, UV radiation, and moderate acids. NBR, developed around the same period, blends butadiene and acrylonitrile, creating a polymer chain with high polarity—this is what repels oils and solvents.
Chemical Structures and Properties
- Neoprene: –[CH₂–C(Cl)=CH–CH₂]–
- Contains 35–38% chlorine by weight
- Moderately polar, offering moderate oil resistance
- NBR: –[CH₂–CH=CH–CH₂]–[CH₂–CI–CH=CH₂]– (acrylonitrile units ~18–50%)
- Acrylonitrile units increase polarity
- Excellent oil and hydrocarbon resistance
Is Neoprene the Same as NBR?
No. While both are synthetic rubbers, Neoprene’s chlorine atoms confer weather resistance that NBR cannot match, and NBR’s high acrylonitrile content gives it oil resistance far beyond Neoprene’s capabilities.
Typical Formulations
Manufacturers adjust crosslink density, fillers (carbon black, silica), and plasticizers to tailor hardness (Shore A 30–90), tensile strength (8–25 MPa), and elongation (200–650%).
- Neoprene Grades: CR-50, CR-70, CR-90
- NBR Grades: NBR-18, NBR-33, NBR-50 (acrylonitrile content)
Understanding these fundamentals lets you predict cost, performance, and lifespan—crucial when Szoneier offers low-MOQ custom runs starting at 50 pieces with rapid sampling and free samples.
What Chemical and Oil Resistance Differences Exist Between Neoprene and NBR?
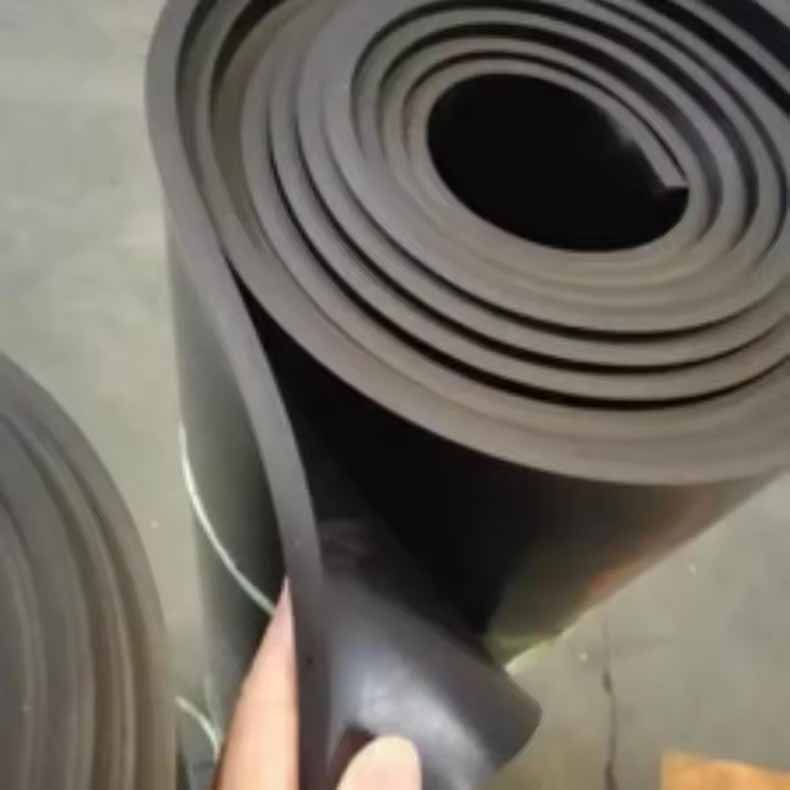
Neoprene resists mild oils and greases but degrades under strong hydrocarbons. NBR, especially with ≥33% acrylonitrile, withstands a wide range of oils, fuels, and solvents. For petroleum-based applications, NBR is superior; for general-purpose sealing with occasional oil exposure, Neoprene offers acceptable performance.
Chemical compatibility determines seal life, maintenance cycles, and failure risk. NBR’s acrylonitrile content provides intermolecular dipoles that repel nonpolar hydrocarbons, enabling stable performance in gear oils, diesel, and synthetic lubricants. By contrast, Neoprene’s chlorine sites enhance resistance to ozone and weathering but offer only moderate compatibility with oils.
Property | Neoprene (CR-50) | NBR (NBR-33) |
---|---|---|
Resistance to Mineral Oil | Up to ISO VG32 oils | Up to ISO VG150 oils |
Fuel Resistance | Weak (swelling >30% in gasoline) | Strong (swelling <20% in gasoline) |
Solvent Resistance | Moderate (ketones attack) | Excellent (resists ketones, some esters) |
- Mineral Oils & Greases
- Neoprene: Acceptable for light gear oils, low-viscosity greases; swelling 10–20% after 72 h.
- NBR: Designed for heavy oils; swelling <5% under similar conditions.
- Fuels & Solvents
- NBR excels in petroleum-based fluids; however, high-percentage acrylonitrile grades can become brittle in low temperatures.
- Neoprene fails in aromatic solvents (e.g., toluene) and rapidly swells in gasoline.
- Acids, Bases & Water
- Neoprene: Superior in dilute acids, alkalis; resists hot water immersion.
- NBR: Vulnerable to strong acids; chlorine groups in Neoprene provide better hydrolytic stability.
Critical thinking: If your design calls for fuel-handling hoses in cold climates, NBR’s brittleness could pose risk. A dual-layer approach—NBR inner seal for oil contact, Neoprene outer layer for weathering—can balance performance and cost, showcasing Szoneier’s custom lamination capabilities.
How Do Temperature Resistance and Aging Properties Compare Between the Two?
Neoprene withstands –40 °C to +120 °C, resists ozone and UV, and exhibits minimal compression set over time. NBR’s range is narrower (–30 °C to +100 °C) and it degrades faster under sunlight and ozone. For outdoor or high-temperature service, Neoprene provides longer aging life.
Operating temperature and aging directly affect maintenance intervals and safety margins. Neoprene’s chlorine atoms create crosslink structures that resist thermal oxidation, reducing hardening and cracking over long exposures.
- Low-Temperature Flexibility
- Neoprene: Maintains flexibility to –40 °C; suitable for cold-climate seals.
- NBR: Below –30 °C, increasing stiffness risks seal leaks.
- High-Temperature Stability
- Neoprene: Continuous service up to 120 °C; occasional spikes to 130 °C.
- NBR: Limits around 100 °C; above this, rapid embrittlement and compression set increase.
- Ozone & UV Resistance
- Neoprene: Excellent (100 pphm ozone chamber, 168 h, no cracks).
- NBR: Poor; micro-cracks form within 72 h under similar conditions.
- Compression Set & Long-Term Aging
- After 70 h at 100 °C under 25% deflection:
- Neoprene: ≤25% set
- NBR: ≥40% set
- This gap widens with time, making Neoprene preferable for dynamic seals.
- After 70 h at 100 °C under 25% deflection:
Case study: An electronics firm replaced NBR gaskets in solar junction boxes with Neoprene ones, extending service life by 30 % in desert environments—an insight Szoneier’s engineers uncovered during rapid prototyping.
Which Material Offers Better Mechanical Strength and Durability?
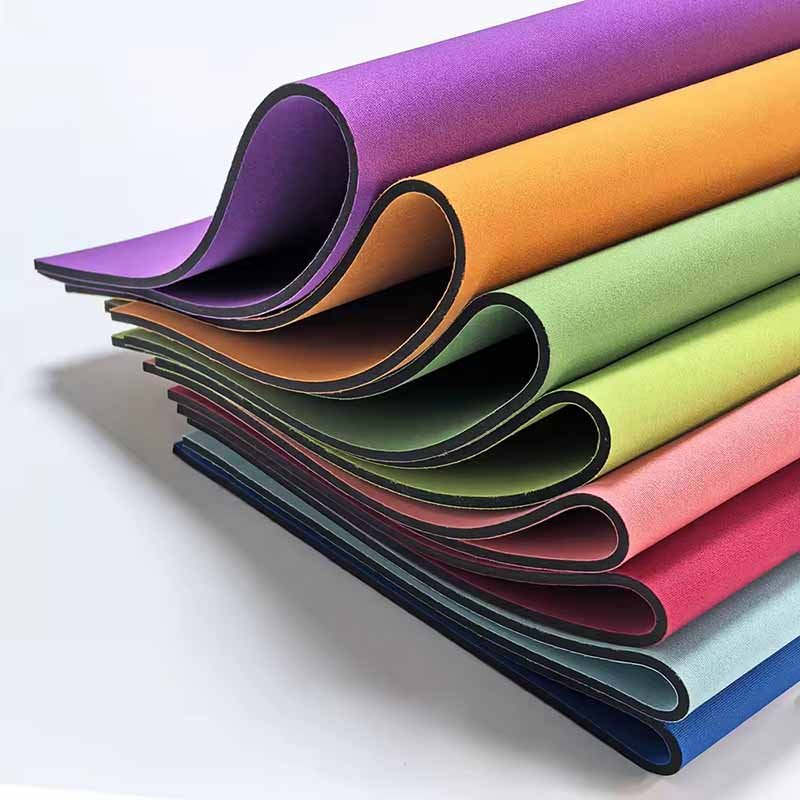
Neoprene typically delivers tensile strength of 8–13 MPa and elongation of 200–600%. NBR’s tensile strength ranges 10–24 MPa with elongation 400–650%. While NBR often shows higher tensile strength, Neoprene offers better tear and abrasion resistance in harsh environments.
Mechanical strength dictates load-bearing capacity, abrasion life, and tear resistance—key for dynamic components.
- Tensile Strength & Elongation
- Neoprene: 8–13 MPa, elongation 200–550%.
- NBR: 10–24 MPa, elongation 300–650%. High acrylonitrile NBR grades approach 24 MPa but lose flexibility at low temperatures.
- Tear Resistance
- Neoprene: 30–60 kN/m
- NBR: 25–55 kN/m Neoprene’s chlorine crosslinks dissipate crack propagation better.
- Abrasion & Fatigue
- Under repetitive flex cycles (1 Hz, 25% strain):
- Neoprene retains 80 % original thickness after 1 million cycles.
- NBR retains 65 %.
- Under repetitive flex cycles (1 Hz, 25% strain):
Is Neoprene Stronger Than Nitrile?
Strength depends on grade: high-acrylonitrile NBR can exceed Neoprene in tensile tests, but Neoprene’s balance of tear, fatigue, and environmental durability often makes it “stronger” in real-world, multi-stress applications.
Critical Perspective
While highest-strength NBR might appeal for static load seals, dynamic applications—like neoprene bags or wetsuits—benefit from Neoprene’s tear and abrasion profile. Szoneier’s custom compounding optimizes both materials to your load cycle and environmental demands.
Are There Cost and MOQ Considerations for Neoprene vs NBR in Bulk Manufacturing?
Raw Neoprene compounds cost ~10–20% more per kilogram than NBR, due to chloroprene monomer expense. However, Neoprene’s longer service life can lower lifecycle costs. MOQ for custom sheets or molded parts typically starts at 50 pieces for both, with lead times of 7–10 days for samples and 20–25 days for production.
Upfront material cost isn’t the whole story—tooling, order size, and total cost of ownership shape your bottom line.
- Raw Material Pricing
- Neoprene: $4.50–$6.00/kg (CR-50 to CR-90)
- NBR: $3.50–$5.00/kg (NBR-18 to NBR-50)
- Tooling & Setup
- Injection molds or die-cut tools: $1,000–$5,000 one-time.
- Szoneier amortizes tooling across small runs—50–100 units—keeping initial investment low.
- MOQ & Lead Time
- Both compounds: MOQ = 50 units; free samples available.
- Sampling: 5–7 days; mass production: 20–30 days.
- Lifecycle & Warranty Costs
- Neoprene’s extended aging life can reduce warranty claims by up to 30%.
- NBR’s superior oil resistance may cut maintenance in petrochemical plants by 15%.
By evaluating total cost—not just material price—you’ll find a balanced ROI. Szoneier’s transparent cost breakdowns let you compare scenarios side by side before committing.
How Do Customization and OEM/ODM Services Differ for Neoprene vs NBR Products?
Both Neoprene and NBR can be custom-colored, cut, and printed with logos. Neoprene offers wider color palettes and embossed textures, while NBR’s chemical resistance limits pigment options. Sampling speed is identical—5–7 days—and Szoneier provides free digital proofs and samples to validate fit, finish, and performance.
Customization drives brand recognition and product differentiation. Understanding material-specific constraints maximizes impact.
- Color & Texture
- Neoprene: Pantone-matched pigments, matte or glossy finishes, embossed patterns, and laminated fabrics (e.g., nylon/neoprene sandwiches).
- NBR: Limited to darker colors—high pigment load can compromise oil resistance; matte finish only.
- Printing & Branding
- Silk-screen, heat-transfer, UV printing:
- Neoprene accepts up to 10 colours with crisp edges.
- NBR limits to 2–4 colours; screening must use compatible inks.
- Silk-screen, heat-transfer, UV printing:
- Fabric Lamination & Bonding
- Neoprene readily bonds to polyester, nylon, metal films—ideal for bags, pouches, and protective covers.
- NBR bonding is trickier—requires primer, limiting multi-material assemblies.
- Sampling & Iteration
- Digital mockups, laser-cut prototypes in 5 days.
- Free physical samples—test fit, feel, and performance before full runs.
- OEM/ODM Process
- Szoneier’s turnkey service: concept → design → prototyping → pilot run → mass production.
- Technical support on material selection, regulatory compliance (RoHS, REACH, FDA).
Whether you need a printed neoprene koozie for promotions or an NBR gasket for fuel pumps, our team ensures your logo, color, and performance specs are met with precision.
What Are the Top Industrial Applications for Neoprene vs NBR?
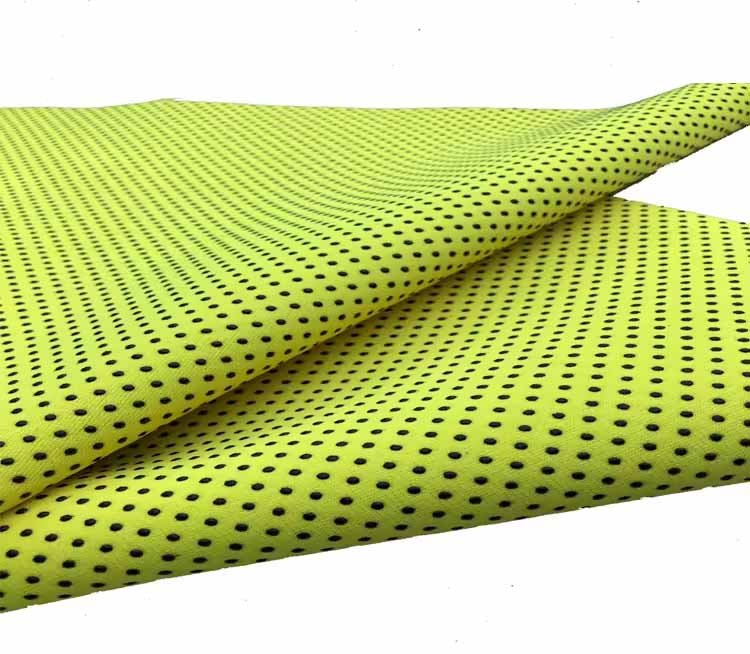
Neoprene shines in marine gear, wetsuits, and weather-exposed seals. NBR dominates automotive hoses, fuel-system seals, and oil-resistant gaskets. Each excels where its specific resistance profile aligns with functional demands—making application context the ultimate selection driver.
Understanding where each rubber thrives lets you optimize product portfolios:
- Automotive
- NBR: Fuel hoses, O-rings, gaskets—handles gasoline, diesel, brake fluids.
- Neoprene: Radiator hoses (coolant), vibration dampers, wiper blade seals.
- Marine & Waterproof Gear
- Neoprene: Wetsuits, dry-bag pouches, boat fenders—UV, saltwater resistance.
- NBR: Under-hull gaskets—brief oil exposure but minimal UV demand.
- Medical & Food Processing
- NBR: Disposable gloves, tubing—biocompatible grades resist blood, oils, and sterilization.
- Neoprene: Strap and bandage materials—reusable, washable, moderate chemical exposure.
- Electronics & Insulation
- Neoprene: Cable jacketing, protective cases—flame retardancy, weather sealing.
- NBR: Potting seals in fuel-level sensors—primary oil contact, low UV.
- Industrial Machinery
- Both materials appear in hydraulic seals; NBR for high-pressure oil, Neoprene for cylinder rod wipers.
Critical lens: Some hybrid designs pair NBR’s inner oil-resistance with Neoprene’s outer weather barrier—maximizing lifespan in outdoor oil-transfer units.
How Do You Select the Right Rubber for Your Specific Application?
Choose Neoprene for UV, ozone, and broad-temperature stability; choose NBR for superior resistance to oils, fuels, and solvents. Balance performance, cost, and lifecycle requirements using a simple checklist: environment, chemical exposure, mechanical demands, and budget.
- Environmental Factors
- Outdoor/UV → Neoprene
- Submerged/Oil-rich → NBR
- Temperature Range
- –40 °C to +120 °C → Neoprene
- –30 °C to +100 °C → NBR
- Chemical Exposure
- Hydrocarbons & Fuels → NBR
- Acids, Alkalis, Weathering → Neoprene
- Mechanical Requirements
- High Tensile Strength → NBR
- High Tear & Fatigue Resistance → Neoprene
- Cost & Lifecycle
- Lower Upfront Cost → NBR
- Lower Maintenance/Warranty → Neoprene
- Customization Needs
- Vibrant Colors & Textures → Neoprene
- Basic Logos & Dark Shades → NBR
Which Is Better: Neoprene or Rubber?
“Better” depends on context: for oil-system components, NBR is unmatched; for outdoor or dynamic sealing, Neoprene is king. Your specific application scenario drives the decision.
Ready to Optimize Your Next Project?
Partner with Szoneier—an 18-year veteran neoprene and NBR manufacturer offering free design, low MOQ (starting at 50 pcs), rapid sampling, and turnkey OEM/ODM services. Whether you need neoprene bags, NBR gaskets, or hybrid solutions, our expert team ensures top-tier quality, on-time delivery, and competitive pricing.
Contact us today to discuss your custom formulation, branding, and volume needs. Let’s engineer the perfect rubber solution for your product!