Neoprene sleeves have quietly become the unsung heroes in industries ranging from electronics to beverage packaging. Imagine sliding your water bottle into a soft, flexible jacket that not only cushions it against bumps but also keeps your drink cooler for longer. Now, picture that same material wrapped around delicate cables or even luxurious cosmetic containers—neoprene sleeves do it all. Their versatility stems from a unique balance of elasticity and structural strength, making them ideal for products that demand both form and function.
A neoprene sleeve is a protective covering made from synthetic rubber, prized for its cushioning, thermal insulation, and customizability—ideal for safeguarding electronics, bottles, and tubing while reinforcing brand identity.
But what exactly makes neoprene so special? In this article, you’ll learn which neoprene grades suit specific applications, how sleeves are manufactured, and the key performance tests that guarantee durability. We’ll also explore customization options—logos, patterns, colors—to elevate your brand’s visibility. Finally, I’ll share insider tips on caring for your sleeves to ensure they last as long as your clients need them. Ready for the deep dive? Let’s unravel the science, design, and marketing secrets behind neoprene sleeves—and see why Szoneier is the partner you need for custom solutions.
What Exactly Is a Neoprene Sleeve and Why Is It So Versatile?
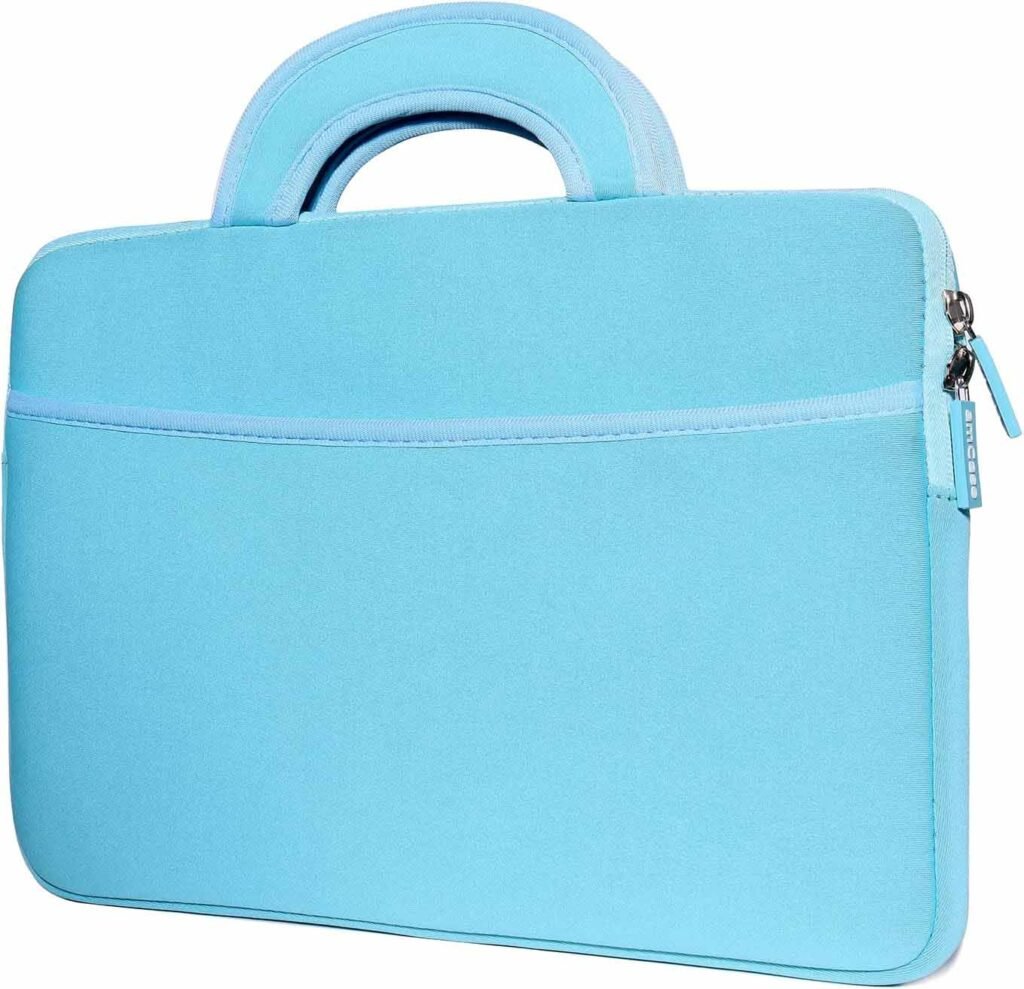
A neoprene sleeve is a form-fitting cover crafted from synthetic rubber (neoprene) designed to protect items from shock, moisture, and temperature fluctuations. Its flexibility, durability, and ease of customization make it suitable for electronics, bottles, tubing, and more, giving businesses a lightweight yet robust solution to safeguard products and reinforce brand messaging.
Neoprene, developed in the 1930s by DuPont, is a family of synthetic rubbers known for resilience, elasticity, and resistance to environmental factors like ozone, UV light, and chemicals. When fabricated into sleeves, neoprene combines these intrinsic properties with engineered thickness and texture to cater to diverse industry needs.
- Shock and Impact Protection At its core, a neoprene sleeve acts as a buffer against physical shocks. The closed-cell foam structure traps tiny gas bubbles that compress under impact, dispersing energy away from the protected item. For electronics—such as hard drives or mobile phones—this cushioning can be the difference between a functional device and a costly replacement. In lab settings, neoprene sleeves even safeguard delicate sensors during transport.
- Thermal Insulation Neoprene’s low thermal conductivity makes it an excellent insulator. When used for beverage sleeves (koozies), it slows heat exchange, keeping drinks colder up to 30% longer than without insulation. In industrial applications, sleeves around piping or tubing reduce heat loss and protect workers from hot surfaces.
- Moisture and Chemical Resistance Unlike natural rubber, neoprene resists water absorption and chemical attack. A sleeve on outdoor wiring harnesses prevents water ingress and corrosion. In marine environments, neoprene sleeves on cable assemblies withstand saltwater spray for over 1,000 hours of continuous exposure without significant degradation.
- Customizability and Branding Neoprene’s smooth surface accepts screen printing and heat transfers readily. Brands can apply vivid logos, patterns, and promotional messages directly onto the sleeve. Whether you’re launching a limited-edition product or offering private-label packaging, neoprene sleeves double as mobile billboards that travel with your customers.
- Versatility Across Industries
- Consumer Goods: Laptop, tablet, and e-reader sleeves
- Food & Beverage: Can coolers, bottle insulators
- Healthcare: Protective covers for medical tubing
- Industrial: Insulation for hoses, wires, and pneumatic lines
- Sporting Goods: Padding for bike frames, ski poles, or fishing rods
By tailoring neoprene formulations—adjusting nitrile content, crosslink density, or adding fire-retardant fillers—manufacturers like Szoneier can fine-tune sleeves for chemical exposure, flame resistance, or extreme temperatures. This chameleon-like adaptability is why neoprene sleeves remain a go-to solution across sectors.
Which Neoprene Grades and Thicknesses Best Suit Different Sleeve Applications?
Neoprene comes in grades from 18A to 60A (shore hardness) and thicknesses ranging 0.5–10 mm. Soft grades (18A–30A) with 2–4 mm thickness excel for beverage insulators, while firmer grades (40A–60A) at 3–6 mm are ideal for cable protection and industrial sleeves requiring structural support.
Choosing the right neoprene grade and thickness hinges on balancing flexibility, durability, and insulation:
- Understanding Shore Hardness
- 18A–30A (Soft): Highly pliable, excellent for form-fitting applications such as bottle sleeves or cosmetic packaging. Soft grades conform snugly but offer limited structural rigidity.
- 40A–50A (Medium): The “workhorse” range for general-purpose sleeves. Offers enhanced tear resistance and moderate stiffness—ideal for electronic device cases or tubing protection.
- 60A (Firm): Near-rigid, suited for heavy-duty industrial sleeves that resist deformation under load, such as hydraulic hose covers.
- Optimizing Thickness Application Recommended Thickness Benefits Beverage insulators (koozies) 2–4 mm Good thermal barrier, lightweight Electronic device sleeves 3–5 mm Balanced padding and form retention Industrial hose/cable sleeves 4–8 mm Excellent impact resistance, durability High-temperature insulation 6–10 mm Superior thermal protection under extreme heat
- Trade-offs and Customization
- Thicker sleeves improve shock and heat resistance but reduce flexibility and increase material cost.
- Thinner sleeves save weight and cost but may not protect adequately against impact or temperature extremes.
- Composite constructions—for example, neoprene laminated to polyester or nylon fabric—add tear resistance and aesthetic options without excessive bulk.
- Case Study: Electronics vs. Beverage A tablet sleeve at 4 mm, 45A neoprene offers a perfect cushion without adding substantial bulk to a backpack. Conversely, a 3 mm, 25A neoprene koozie clamps tightly to a can, maximizing insulation while remaining pocket-friendly.
- Rapid Sampling and Low MOQ Szoneier provides free sample prototyping across grades and thicknesses. By testing 2–3 variants, you can quickly identify the sweet spot for your product’s protective and branding needs—saving both time and budget before full-scale production.
How Are Neoprene Sleeves Manufactured—from Raw Material to Finished Product?
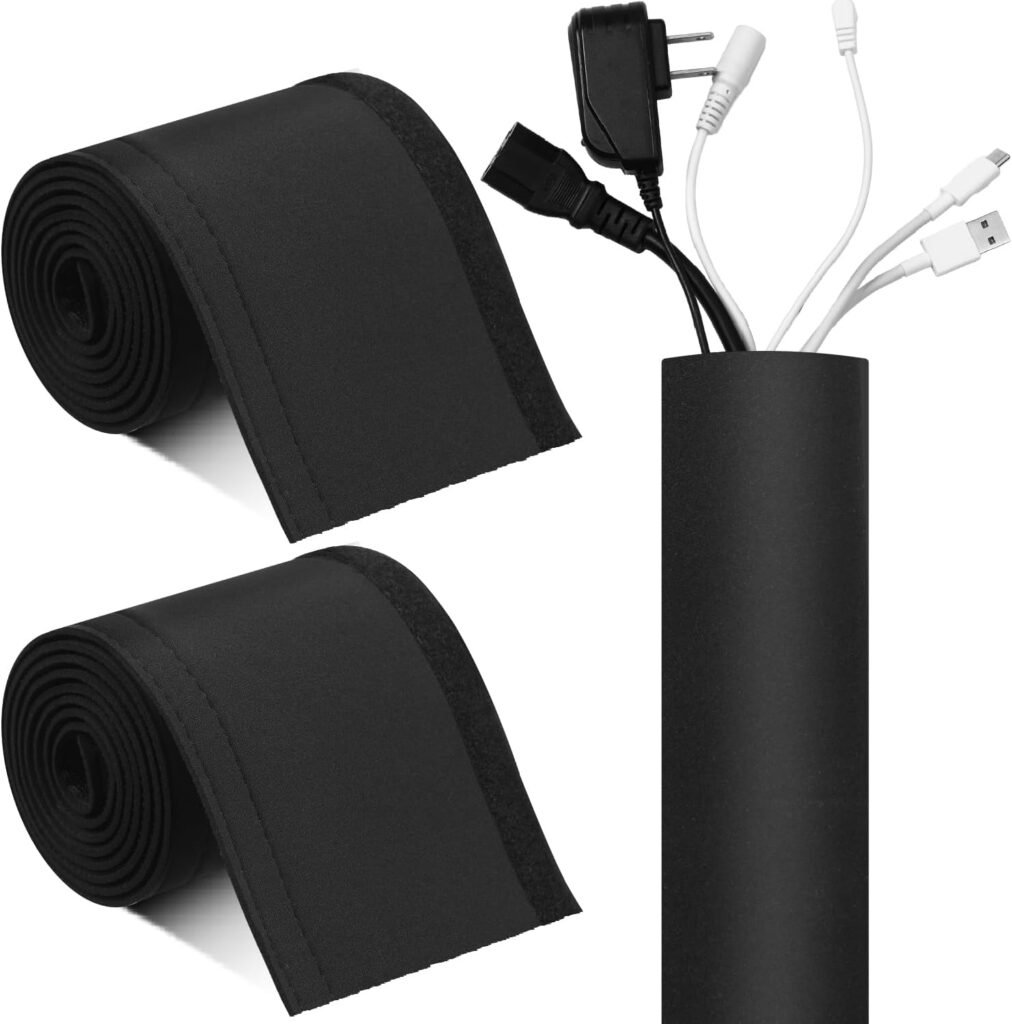
Neoprene sleeves are produced by calendaring or extrusion of neoprene sheets, followed by die-cutting, heat-sealing or stitching, and printing. Custom linings, laminations, and finishing processes—like laser cutting or ultrasonic welding—ensure precision, consistent tolerances, and high production speed.
The journey from raw neoprene compound to finished sleeve involves several critical stages:
- Compounding and Sheet Formation
- Mixing: Base polymers, fillers (carbon black, silica), and curing agents are blended in a Banbury mixer. Additives—UV stabilizers or flame retardants—tailor performance.
- Calendering/Extrusion: The compound is formed into uniform sheets of specified thickness via calender rolls or extruded through a flat die. Strict temperature and tension control maintain thickness tolerances within ±0.1 mm.
- Lamination (Optional)
- To enhance tear strength and aesthetics, neoprene sheets can be laminated with knitted polyester, nylon tricot, or mesh fabrics. Adhesive systems ensure strong bonding without compromising flexibility.
- Cutting and Die-Cutting
- Manual CAD-to-Cut: Digital patterns (DXF files) guide CNC die-cutting or laser cutting machines for precise shapes—eliminating edge fraying common in manual cutting.
- Tooling: Low-cost metal rule dies are ideal for large volumes; laser cutters shine for rapid prototyping and small batches.
- Sealing and Stitching
- Heat-Sealing/Welding: Ultrasonic or hot-air welding fuses neoprene edges, creating watertight seams without threads—critical for beverage or medical applications.
- Overlock Stitching: Nylon or polyester threads provide flexible, durable seams. Flatlock stitches minimize chafing and bulk.
- Printing and Finishing
- Screen Printing: Applies solid-color logos or patterns—cost-effective for runs over 500 units.
- Heat Transfer: Offers photographic quality and unlimited color options—perfect for small batches or multi-color designs.
- Edge Binding: Optional nylon binding adds contrast trim and extra durability at high-wear edges.
- Quality Control
- Dimensional Checks: Random sleeves undergo caliper measurement for thickness and dimensional accuracy.
- Tensile and Tear Tests: ASTM D412 and D624 standards ensure the neoprene meets strength specifications.
- Ageing and UV Exposure: Accelerated weathering chambers simulate long-term environmental exposure to guarantee performance.
By leveraging Szoneier’s vertically integrated facilities—mixing, calendering, lamination, printing, and sewing all under one roof—lead times can be as short as 7–10 days. Low MOQs (starting at 50 pieces) let you validate your design before scaling up, while free sample services eliminate initial tooling costs.
What Protective and Insulating Properties Do Neoprene Sleeves Provide?
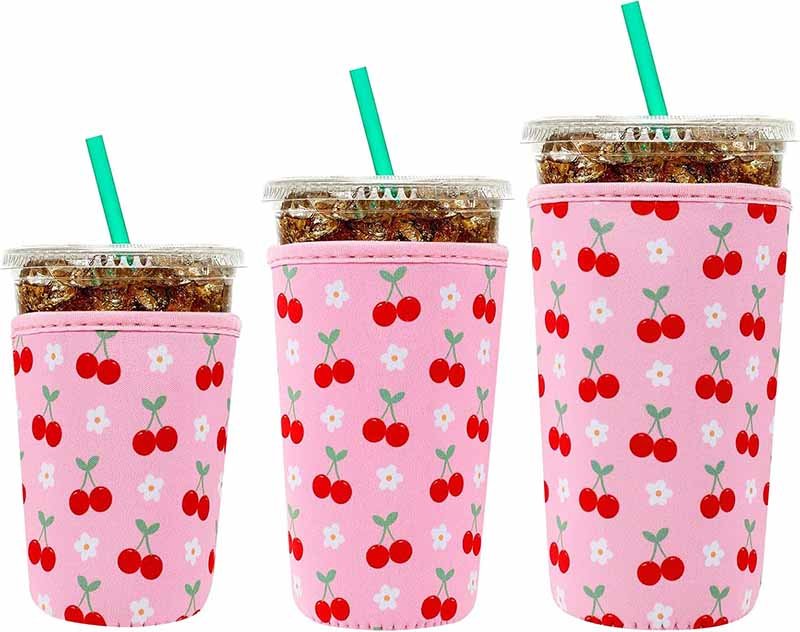
Neoprene’s closed-cell foam structure delivers up to 30% better shock absorption than EVA foam and reduces heat transfer by 25–35%. Its moisture resistance and UV stability make sleeves ideal for wet or outdoor environments, while custom flame-retardant grades meet UL94 V-0 requirements for electronic housings.
Neoprene sleeves owe their protective prowess to a combination of material science and engineered structure:
- Shock Absorption Metrics
- Energy Dissipation: Standard neoprene dissipates ~8 kPa energy under 50% compression—higher than many competing foams. This translates to reduced peak forces transmitted to devices during drops or impacts.
- Rebound Resilience: Over 80% rebound rate after repeated compression cycles ensures sleeves don’t bottom out over time.
- Thermal Performance Property Neoprene Sleeve (4 mm) Plain Air Thermal Conductivity (W/m·K) 0.055 0.026 Temperature Drop Over 30 min 6 °C 15 °C Recommended Operating Range –40 to 120 °C – In real-world tests, 4 mm neoprene slows heat gain by over 60% compared to a bare aluminum container, making it invaluable for beverage sleeves and insulated tubing.
- Moisture and Chemical Resistance Neoprene absorbs less than 3% water by weight when submerged for 24 hours, preventing mold growth and maintaining insulating properties. Grades with nitrile content resist oils, fuels, and solvents—perfect for hydraulic hose covers in industrial settings.
- UV and Ozone Stability Extended exposure to UV and ozone can degrade many rubbers. Neoprene sleeves treated with anti-ozonants retain over 90% tensile strength after 1,000 hours in an accelerated weathering chamber, ensuring longevity for outdoor signage or marine cables.
- Fire and Flame Retardancy UL94 V-0 neoprene compounds self-extinguish within 10 seconds of flame removal, with no dripping. This is critical for electronic device housings and medical equipment covers, where fire safety standards are stringent.
By selecting the right combination of grade, thickness, and additives, you can tailor neoprene sleeves to meet or exceed industry-specific protection benchmarks. Szoneier’s lab facilities can certify performance through standardized testing, giving you confidence in every batch.
How Do You Choose the Right Neoprene Sleeve for Electronics, Bottles, or Tubing?
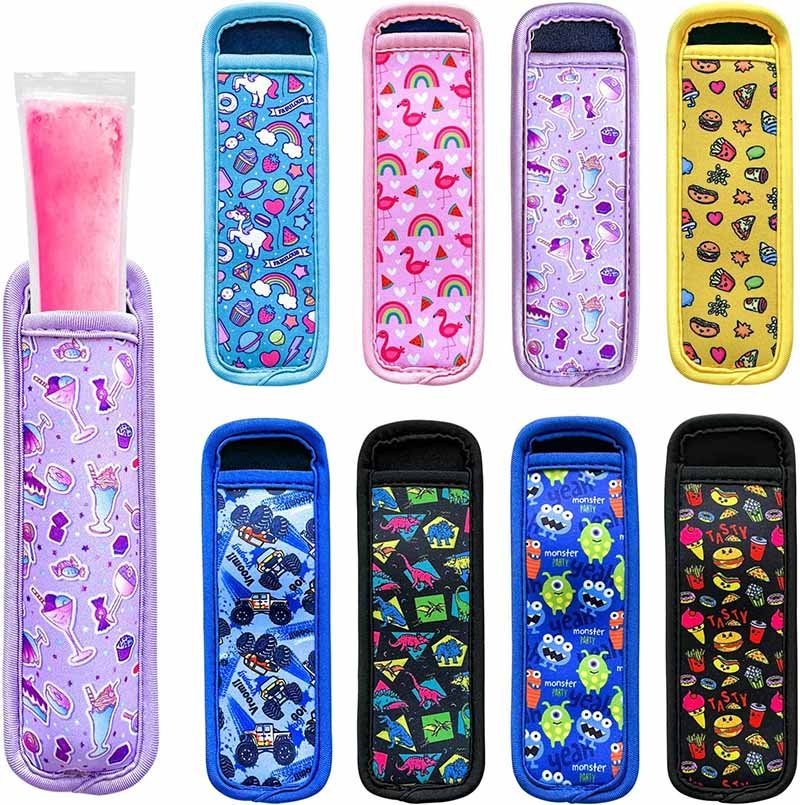
Match sleeve grade, thickness, and finishing to use-case: choose 45A/4 mm for gadgets; 25A/3 mm for drinkware; 40A/5–8 mm with chemical-resistant additives for tubing. Consider seam method—heat-sealed for liquids, stitched for flexibility—and customizable printing to reinforce brand identity.
Selecting the optimal neoprene sleeve requires a holistic assessment of product requirements and end-user expectations:
- Define Primary Function
- Cushioning vs. Insulation: If impact protection is paramount—like for portable hard drives—prioritize higher shore hardness (45A–55A) and 4–6 mm thickness. For cold retention in can coolers, softer grades (20A–30A) at 2–4 mm work best.
- Moisture Barrier: Sleeves for water bottles or medical tubing should be fully sealed. Heat-sealing or ultrasonic welding ensures zero leakage; stitching alone may allow moisture ingress over time.
- Consider End-Use Environment
- Outdoor vs. Indoor: For outdoor cables, choose UV-stabilized neoprene with anti-ozonants. Indoor office sleeves can forego these additives, reducing cost.
- Chemical Exposure: Industrial hoses in contact with oils or solvents need nitrile-modified neoprene grades for resistance.
- Customization and Branding Needs
- Printing Complexity: Simple logos on koozies can use one-color screen printing. Multi-color or photo-quality designs—like promotional event cases—benefit from heat-transferred decals.
- Colorfastness: Ensure printed sleeves use UV-resistant inks to avoid fading under sunlight.
- Prototyping and Sampling Engage with low-MOQ prototyping to compare 2–3 variants. Request Szoneier’s samples in different grades and seam types. Testing prototypes in real-life scenarios uncovers performance nuances often missed on paper.
- Cost and Lead Time
- Material Costs: Premium grades and thicker sheets will raise per-unit costs by up to 20–30%. Laminations or specialized additives (flame retardants) add another 10–15%.
- Turnaround: Szoneier’s rapid sampling service can deliver prototypes in as little as 5 days, with full production run lead times of 10–14 days depending on order size.
By systematically evaluating each factor—function, environment, branding, and budget—you can zero in on the ideal neoprene sleeve that elevates both performance and perception of your product.
Are Neoprene Sleeves Customizable with Logos, Colors, and Patterns?
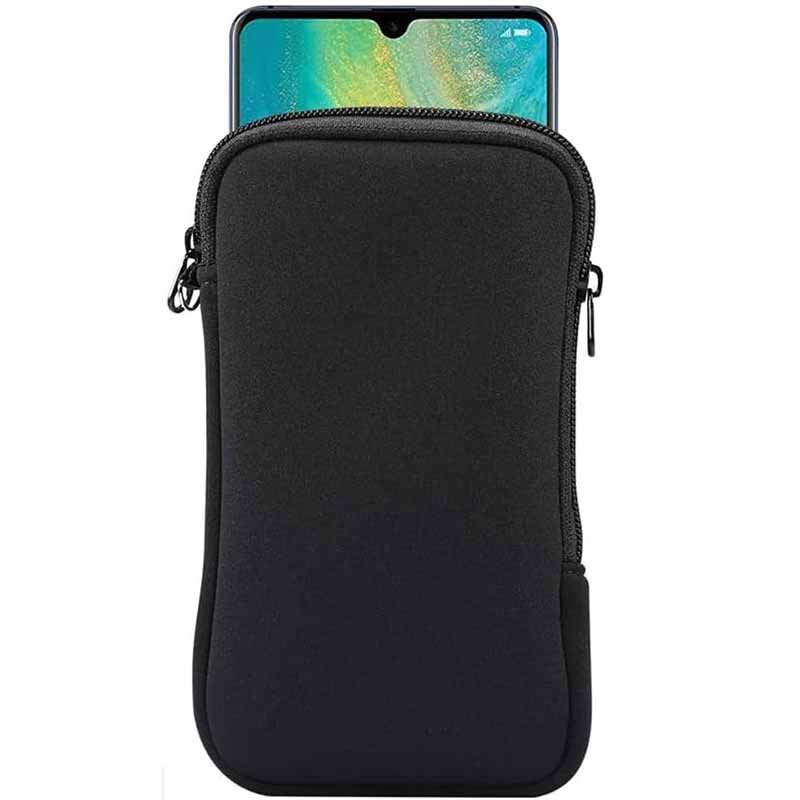
Yes—neoprene accepts screen printing, heat transfers, dye sublimation, and digital printing. You can customize sleeves in unlimited Pantone colors, add all-over patterns, and apply high-definition logos to reinforce brand visibility on every unit.
Neoprene’s smooth, receptive surface makes it a canvas for creative branding:
- Printing Technologies
- Screen Printing: Cost-effective for runs over 500 units. Delivers solid, opaque colors with fast setup. Ideal for one- or two-color logos on standard sleeve shapes.
- Heat Transfer Vinyl (HTV): Applies detailed, multi-color graphics. Best for runs under 300 units or when photographic detail is required. Vinyl thickness adds slight rigidity—consider for flat-case designs.
- Sublimation Printing: Inks are embedded into polyester-lined neoprene, producing vibrant, fade-resistant all-over prints. Requires a polyester-facing; excellent for fashion-forward designs.
- Digital Direct-to-Garment (DTG): Emerging method for small volumes with complex artwork. Offers low setup cost but longer curing times per piece.
- Color Matching and Pantone Szoneier’s in-house Pantone matching ensures your brand colors remain consistent across sleeves, fabrics, and other printed materials. This cohesion strengthens brand recall in the marketplace.
- Pattern and Texture Beyond flat colors, neoprene sleeves can feature embossed textures—like carbon-fiber patterns—or integrated RFID-blocking foil layers. Laminated mesh facings provide breathability and reveal inner contents.
- Edge Trim and Hardware
- Binding Tape: Nylon or polyester binding in contrasting hues adds visual interest while reinforcing high-wear edges.
- Zippers and Pulls: Custom zipper tape and pull-tab colors complement the sleeve body. Metal or plastic hardware can be branded.
- Regulatory and Safety Labels Incorporate permanent ink labels or woven tags for compliance information—especially crucial for medical or food-grade applications. Neo labels resist water, abrasion, and chemical exposure.
By leveraging Szoneier’s advanced printing lines and quality controls, you’ll receive samples with exact color proofs and pattern placements before full-scale runs—minimizing surprises and ensuring every sleeve is a perfect ambassador for your brand.
How Should You Care for and Maintain Neoprene Sleeves to Maximize Lifespan?

Hand-wash neoprene sleeves in lukewarm, mild soapy water; air-dry away from direct sunlight. Avoid bleach, fabric softeners, and high heat. Store flat or rolled, not folded. This routine preserves elasticity, prevents discoloration, and extends service life by up to 50%.
Neoprene sleeves are low-maintenance, but proper care unlocks their full potential:
- Cleaning Protocols
- Regular Cleaning: Rinse with mild detergent diluted in water; gently agitate and rinse thoroughly.
- Stain Removal: Spot-treat with isopropyl alcohol for ink or oil marks; test on an inconspicuous area first to ensure no discoloration.
- Drying Techniques
- Air-Dry Flat: Lay sleeves on a clean towel; avoid hanging, which can stretch edges.
- Avoid Heat Sources: No tumble dryers, radiators, or direct sunlight—high heat degrades neoprene’s crosslink bonds, leading to brittleness.
- Storage Recommendations
- Flat or Rolled Storage: Prevents permanent creases. For tubular sleeves, roll them loosely.
- Avoid Compression: Don’t stack heavy objects on top; prolonged compression can cause indentations or delamination in laminated products.
- Inspection and Repair
- Periodic Checks: Look for seam fraying, delamination, or thinning spots. Early detection allows simple repairs—re-stitching seams or applying liquid neoprene cement.
- Rejuvenation: For lightly aged sleeves, a thin coating of silicone spray can restore surface suppleness and water repellency.
- Expected Lifespan With proper care, neoprene sleeves maintain peak performance for 2–3 years in typical use cases. Harsh environments (UV, chemicals) may reduce this by 30–50%, but rapid replacement is cost-effective given neoprene’s low unit cost.
By following these simple steps, you’ll preserve the protective and aesthetic qualities of neoprene sleeves, ensuring your investments continue to safeguard products and promote your brand over many cycles of use.
What Testing Standards and Quality Checks Ensure Sleeve Performance?
Neoprene sleeves undergo ASTM D412 tensile and elongation tests, ASTM D624 tear resistance, UL94 flammability, and ISO 4589 oxygen index evaluations. Dimensional tolerance checks and 1,000-hour UV/ozone aging simulations verify long-term durability before shipment.
Rigorous testing underpins every high-performance neoprene sleeve:
- Mechanical Properties
- Tensile Strength & Elongation (ASTM D412): Establishes base strength and stretch capacity—critical for sleeves that flex repeatedly. Minimum tensile of 2 MPa and elongation over 300% ensure resilience.
- Tear Resistance (ASTM D624): Measures force to propagate a tear; industrial sleeves often require ≥20 N/mm for heavy-duty applications.
- Thermal and Flammability
- UL94 Vertical Burning Test: Classifies material as V-0, V-1, or V-2. Szoneier’s UL94 V-0 grades self-extinguish within 10 seconds with no dripping.
- Oxygen Index (ISO 4589): Indicates minimum oxygen concentration to sustain combustion; higher values denote better flame resistance.
- Environmental Aging
- UV/Ozone Resistance: Expose samples to 1,000 hours in weathering chambers; measure tensile retention. Quality neoprene retains ≥90% strength post-aging.
- Hydrolytic Stability: Immersion in water at 70 °C for 72 hours tests resilience to mold and swelling.
- Dimensional Accuracy
- Caliper Measurements: Random sampling ensures thickness within ±0.1 mm of specified gauge.
- Pattern Consistency: CNC cutting and die-cut tolerances hold to ±0.5 mm for repeated precision—vital for sleeves that must mate to tight fittings.
- Quality Management Szoneier operates under ISO 9001 protocols, maintaining batch traceability from raw compound to final shipment. Every production lot includes QC certificates detailing test results—delivered alongside product documentation.
By verifying each sleeve against these standards, you guarantee your product’s protective and insulating performance meets or exceeds customer expectations and regulatory requirements.
Conclusion
Neoprene sleeves are the quintessential blend of protection, insulation, and branding flexibility—serving industries from consumer electronics to industrial fluid systems. By understanding neoprene grades, manufacturing processes, performance metrics, and customization options, you can select or design sleeves that perfectly meet your product’s demands and amplify your brand’s visibility in the marketplace.
Ready to prototype your custom neoprene sleeves? Contact Szoneier today for free design consultation, low-MOQ sampling, and rapid lead times. Let our 18+ years of expertise in webbing and neoprene R&D deliver the perfect balance of flexibility and structure for your next product innovation.